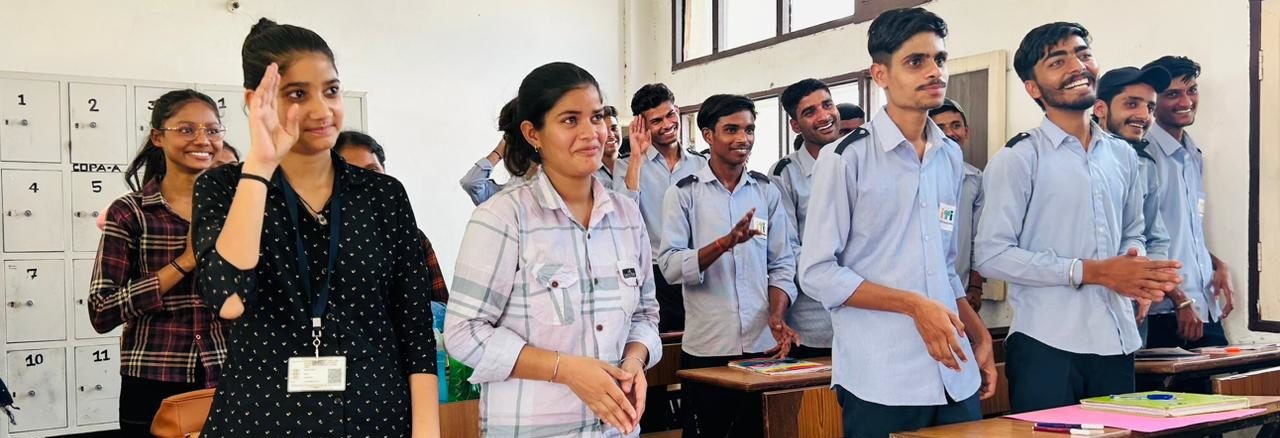
Making on-the-job training work
During industry visits, we often interact with students and alums of Industrial Training Institutes (ITIs) pursuing training or full-time jobs. During one such visit in Haryana, we met Alam*, a resident of Yamuna Nagar, who did his ITI certification in poly plastic operator course in 2016.
Under the national apprenticeship program, Alam obtained an apprenticeship offer to work with ISGEC, one of Haryana’s biggest names in the manufacturing sector. However, after his 6-month long apprenticeship, he struggled to find a job related to his trade.
During this tough time, he also faced a huge personal loss: his father (the sole breadwinner in the family) passed away. Alam took up odd jobs to support his family, working here and there for around 3 years. Finally, he secured employment in Lark Engineering through an ITI campus placement with a monthly salary of INR 16,000.
Are students getting skilled or certified?
Now, the question is, was the struggle to start a stable career merely Alam’s destiny or the indication of a bigger problem in the skill education space? Is India getting skilled, or is it just getting certified?
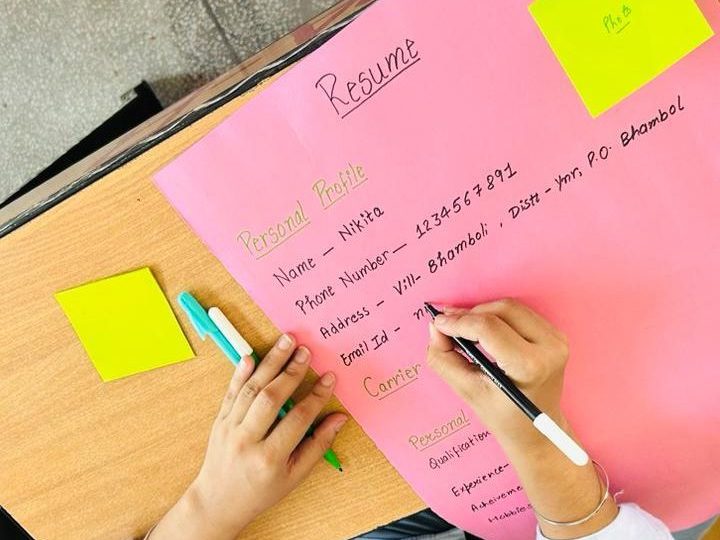
It’s tough getting placed as an ITI student
Every year lakhs of students pass out from 14,789 ITIs across the country, but not many of them get placed:
- As per a recent report (Niti Aayog, 2023, p. 29), the average placement rate of trainees in Indian ITIs is less than 0.1%.
- In 2020, 28,423 trainees passed out from Haryana’s ITIs, but only 2 could secure placements. (Niti Aayog, 2023, p. 34)
Employers struggle to find a skilled workforce
Although there is a massive demand for skilled workforce in industries, there is also a huge gap between the demand and supply of skilled workforce:
- In a diagnostic study conducted by Medha in 2022-23, 85% of industry supervisors responded that lack of theoretical knowledge, interest, and discipline among ITI students were the most common areas of improvement. (Medha, 2020, p4)
- During our industry visits in places like Hero Motocorp, Denso, and Nerolac Kansai, we learned from employers that many ITI students lacked professional etiquette and communication skills.
ITI education system needs more care
ITIs, where students go to build skills, have their bottlenecks, such as inadequate staff strength and outdated curriculum:
- As per the NCVT dashboard, only 48% of the sanctioned instructor positions are occupied.
- Majority of ITIs do not possess the latest tools and equipment for practical training. (Niti Aayog, 2023, p 15)
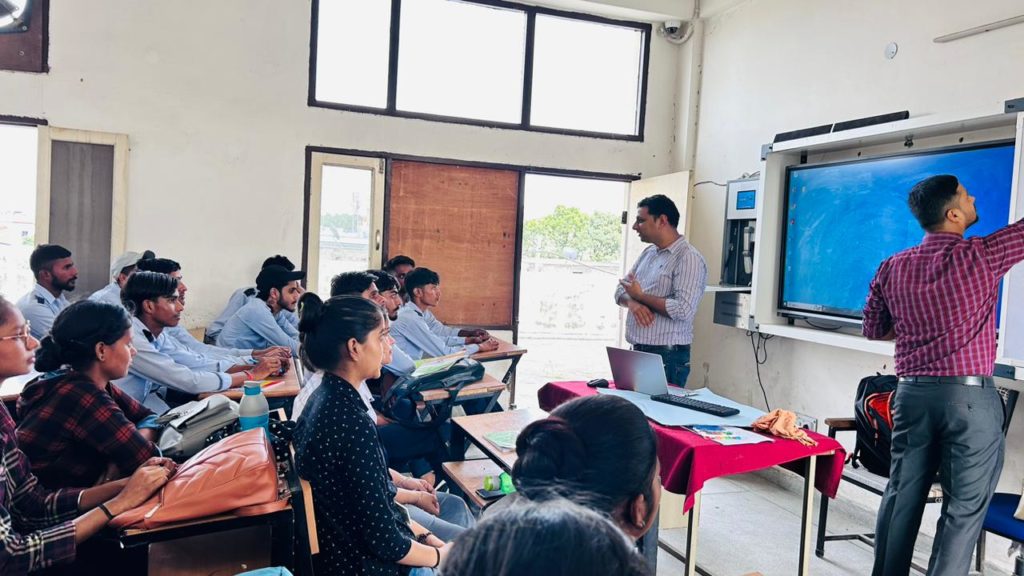
A change in making?
Government studies (such as Sharda Prasad, 2016) suggest making apprenticeship training an integral part of vocational education, in which trainees learn core skills and spend at least a third of the total duration at the company premises. In line with this suggestion, the Ministry of Skill Development and Entrepreneurship (MSDE) introduced the “Dual System of Training” (DST) in 2016.
DST enables industry linkages and provides On-the-Job Training (OJTs) to students on industries’ latest technologies. It bridges the gap between ITI trainees’ learning outcomes and industry requirements.
DST provides On-the-Job Training (OJTs) to students on industries’ latest technologies.
However, when the Government of Haryana actively adopted DST and started DST trades in some ITIs, a few roadblocks affected its effective implementation. After joining DST as an implementation partner, we carried out a diagnostic study that identified some grassroots challenges:
- For OJTs, local contacts were leveraged to sign the MoU, resulting in low-quality industries.
- Despite being a flagship program, most students were unaware of DST.
- Industries faced issues with trainees’ discipline and regularity during OJTs.
We took a few steps to mitigate these challenges throughout our collaboration and have seen encouraging results.
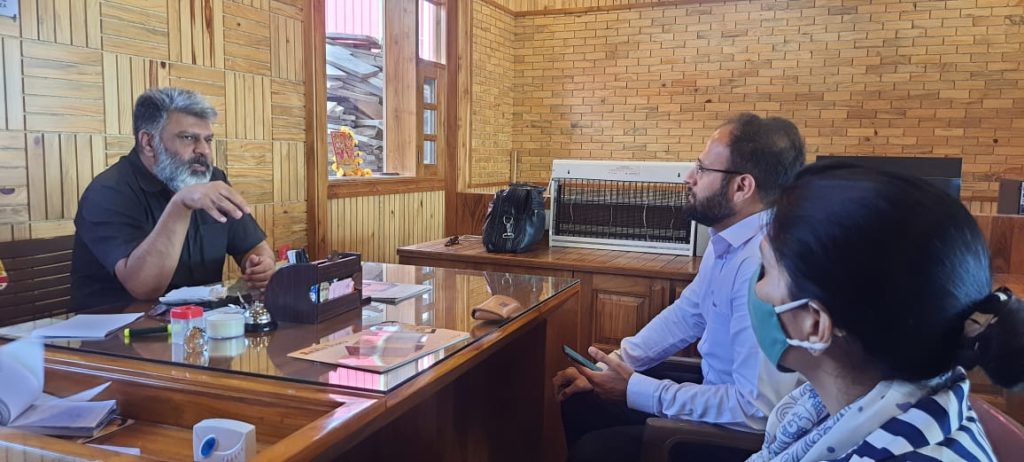
Elevating the quality of industry partnerships
To elevate OJTs, we listed out criteria for shortlisting only quality industry partners. And by sticking to it, we onboarded some large industries like State Sugar Mills, Tata Motors, Nerolac Kansai, Exide, Orient Electric, and Jindal Polybutton. More than 200 eminent industries have partnered with 63 government ITIs of Haryana to provide OJTs to students.
Motivating students as early professionals
To resolve students’ discipline issues, we had to first raise awareness about DST as a career opportunity they could seize to prove themselves and grow. So we conducted pre-OJT workshops on DST’s objective, benefits, and best ways to make the most of it.
We conducted such workshops with 214 ITI trade instructors (who would then go on to orient their students) in 64 ITIs around topics like the power of perception, circle of concern vs. influence, and workplace etiquette. We also directly oriented 1,113 students across 20 districts.
Keeping in touch on the ground
After industry partnerships and workshops, we conducted field visits to OJT premises of industries to understand the real-time challenges of trainees and collect feedback from industry partners.
The field responses indicate that more trainees are getting to do technical tasks related to their trade in the OJT, while more trainers are coming on time and solving students’ issues.
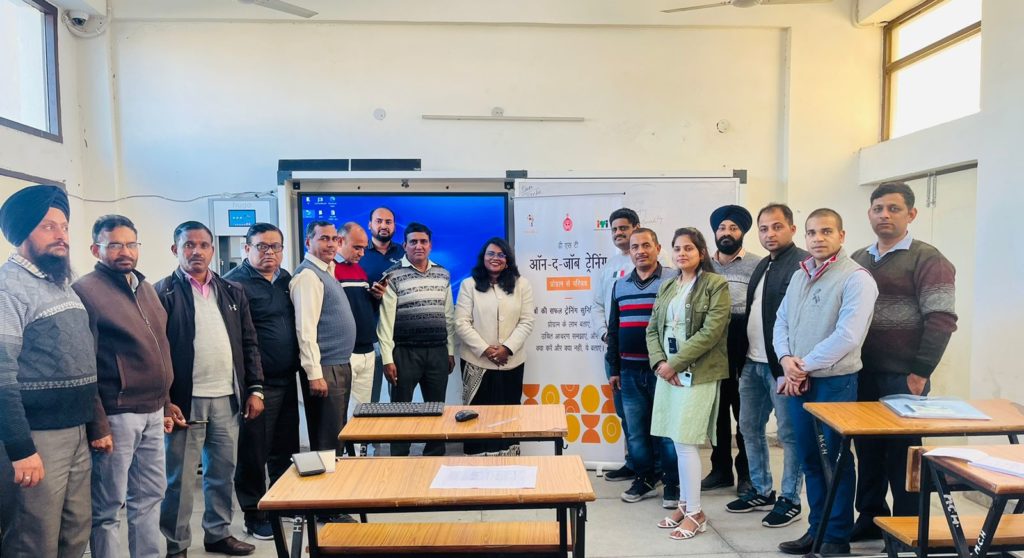
DST: a bridge of hope
An example DST’s impact is the story of Veer*, who secured admission in the carpenter trade from ITI Barwala, Hisar, in 2022.
Under DST, he got an opportunity to work as a trainee at Radha Doors Pvt Ltd for 3 months. During this time, he learned to operate advanced machinery and picked up practical aspects of his trade. Today, he has secured a pre-placement offer to work at Radha Doors for a salary of INR 15,000 per month within a year of enrolling in DST.
DST is a crucial program in skill education. With potentially 4,000 students indirectly impacted through trade instructors, it has multiple stories of transformation that can position Haryana as a model state for implementation and catalyze the ITI system in other states.
As a partner, Medha supports the program’s effective implementation and advocates for better learning outcomes in skill education to live up to the motto: “Kaushal Bharat, Kushal Bharat.”
*names changed.
References:
1. Transforming Industrial Training Institutes, Niti Aayog (2023)
2. Ownership in international vocational education and training transfer: the example of quality development in India, Regel, Ramasamy, Pilz (2022)